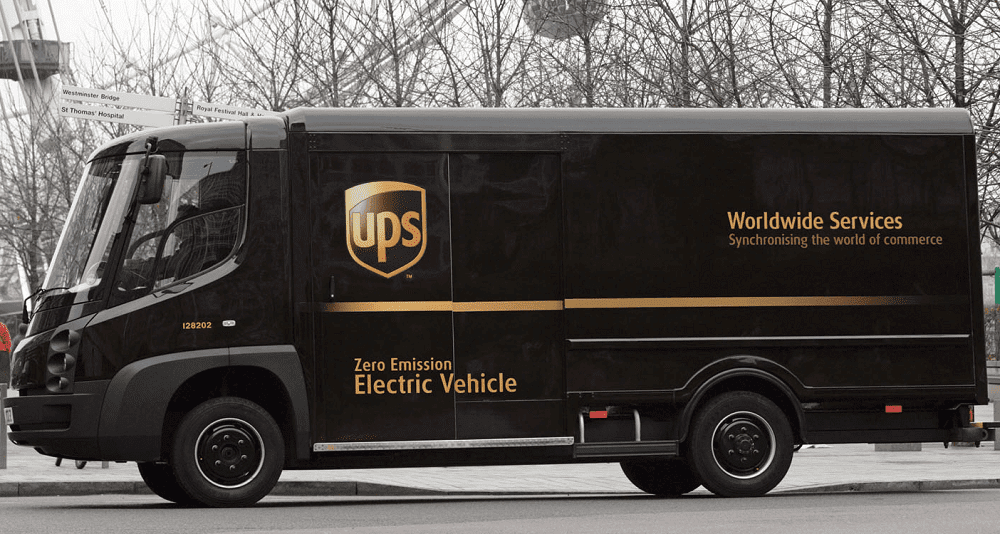
* Miniature Cooling Systems secure performance and longevity in e-vehicles - RIGID HVAC
Overview of the Electric Vehicle Lithium-ion Battery Cooling Technology
Background: The performance of the Lithium battery directly affects the efficiency of the battery pack, and also affects the battery life and safety of use. In order to bring out the best performance and life of the battery pack, it is necessary to optimize the structure of the battery pack, increase the heat dissipation facilities and control the temperature environment of battery operation.
Temperature is an important factor when it comes to Li-ion batteries. They perform best in temperatures between 20 and 30°C, and they also achieve their maximum electrical performance and durability during this temperature range.
Performance will be affected by temperatures that are too high or too low. As the temperature rises above 30°C, the cell oxidation rate increases, resulting in faster battery degradation, and declining performance and capacity. Operation at over 40°C may even cause permanent damage.
The cooling performance of the power battery directly affects its efficiency, and also affects the battery's life and usage safety. As the battery itself generates certain heat during charging and discharging, which leads to the temperature rise, and the temperature rise will affect many characteristics parameters of the battery, such as internal resistance, voltage, SOC, available capacity, charging and discharging efficiency and battery life. So, thermal management is crucial to power battery performance.
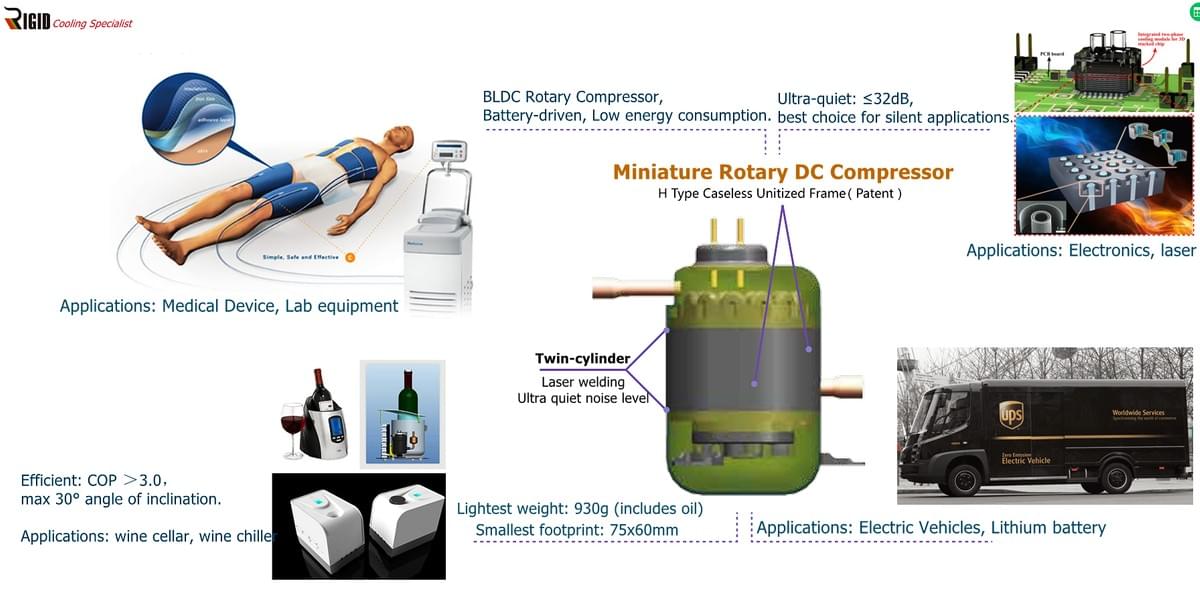
Active Air Cooling
Currently, RIGID Technology micro-cooling systems provide the following cooling approaches for domestic and foreign electric vehicle battery packs: Air Cooling, Liquid Cooling, and Cold Plate Direct Cooling (also name as refrigerant cooling). At present, the air cooling method is still the main method used. Because air cooling is simple configuration and easier to achieve.
RIGID Micro DC Aircon is the world's smallest portable air conditioning module widely used for EVs battery air cooling.
The Micro DC Aircon removes heat from the air which is circulated through the system to cool the heat source. They are especially applied to critical applications where space and weight are important to them. It is widely used for compact and confined space cooling.
The DC Air conditioning systems are ideal for cooling bulk heat loads where minimal modification to the system is desired. The mini compressor air conditioner provides an excellent cooling solution where size/space/efficiency are important factors.
* RIGID Micro DC Aircon provides active and safe air cooling for Lithium-ion battery cooling.
Micro DC Aircon Features:
Compact, Easy to install. Miniature compressor, micro-channel condenser, mini radiator, and fans & blowers are all assembled in-one, No more engineering.
- Low Weight → Extremely Portable
- Low Voltage → Proven Low Risk (12V / 24V / 48V)
- Low Noise → Suitable for Office, Hospital, Home
- Small Footprint → Easily Integrated into Small Spaces
- High Capacity → Comparable to Systems 5x the Size
- High-Efficiency → Low Power Draw, Less Heat Rejection
- High-Reliability → Less Maintenance, Fewer Service Calls
Variable Speed → Accurate Temperature Stability Available
Air-Cooling Battery Thermal Management Systems For EVs and Electric Vehicle Fleets
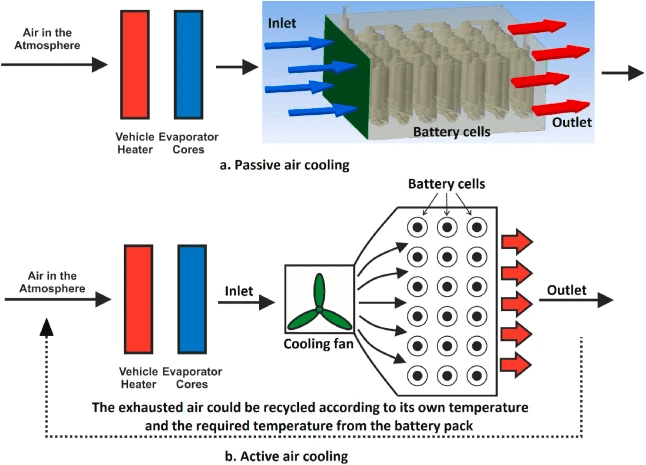
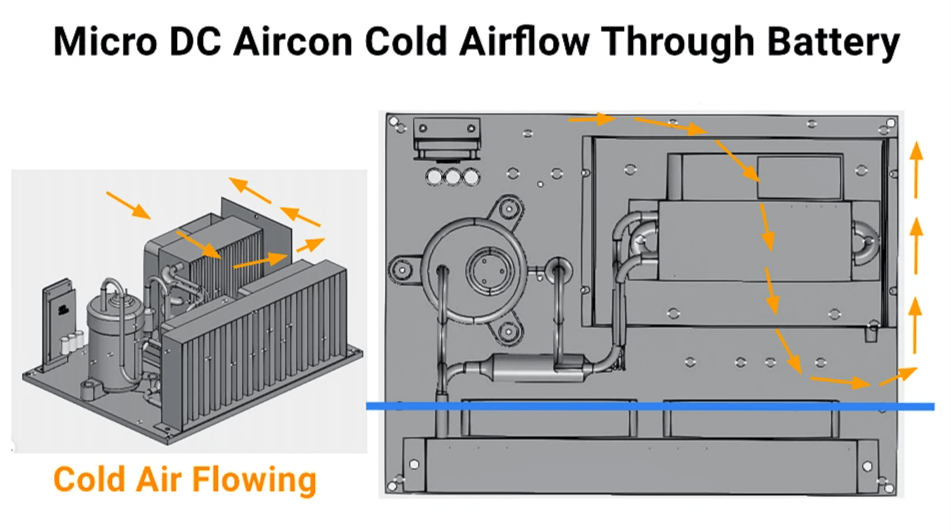
Liquid Fluid Cooling
Although the air cooling approach is widely used in EVs battery thermal management, Air-cooling functionality may not be suitable for tropical areas such as the Middle East and Saudi Arab countries. Especially India’s diverse, and sometimes unusually hot, weather conditions, are range from -5 degrees Celsius to 50 degrees Celsius.
It is known that Li-ion battery operating temperature plays a decisive role in the functionality and especially lifespan of high-performance batteries. Keeping to a constant temperature profile is essential in ensuring long-term performance in EV batteries and stationary energy storage modules. Considering this circumstance, RIGID has developed compact liquid-cooled modules for EV battery packs or electric fleet's portable battery.
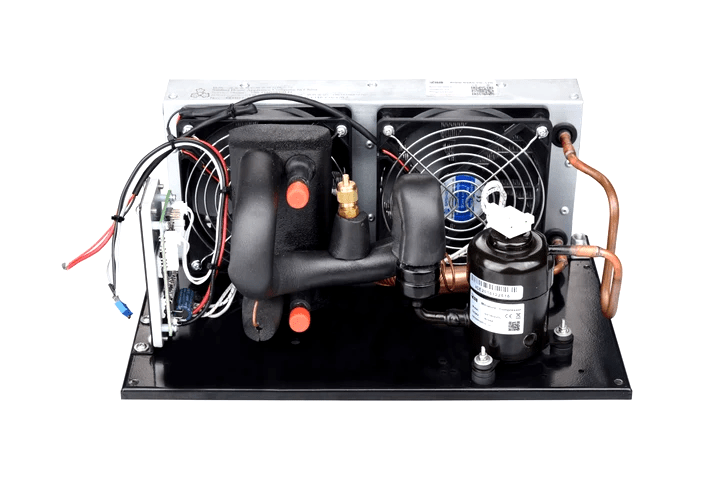
* RIGID Plate Liquid Chiller provides effective cooling performance in battery thermal management.
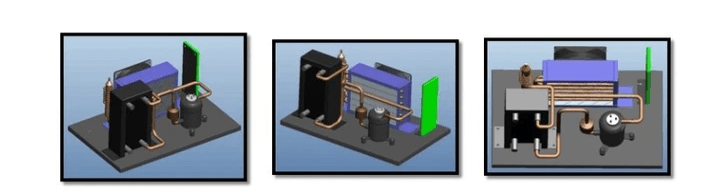
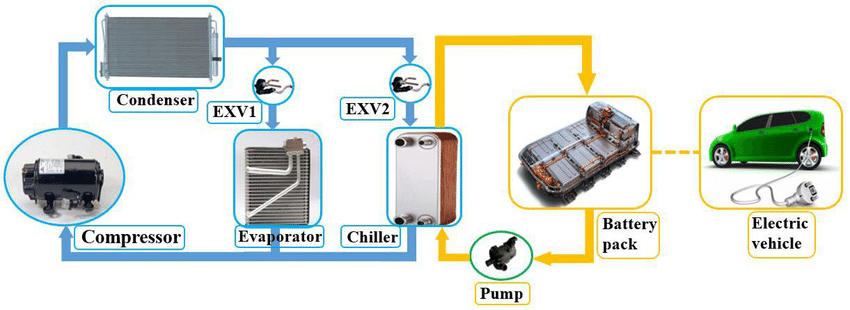
In an electric vehicle battery, current, i.e., charging and discharging, generates heat within the battery and its interconnect system. The higher the current, the more heat is generate. So keeping to a constant temperature profile is essential in ensuring long-term performance in EV batteries and stationary energy storage modules.
Even though fluid cooling is effective for battery temperature cooling down, there is a challenge as far as using liquid cooling in EV is concerned. There is limited real room available in a electric vehicle battery packs system, and integrating a liquid-cooled battery pack is a challenge as you also have to fit in additional components such as pump, reservoir and coolant.
Electric vehicle manufacturers often install liquid cooling systems to keep the constant operating temperature of lithium batteries in the optimal range.
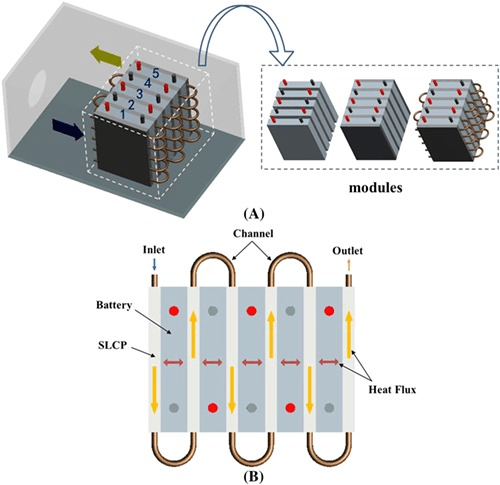
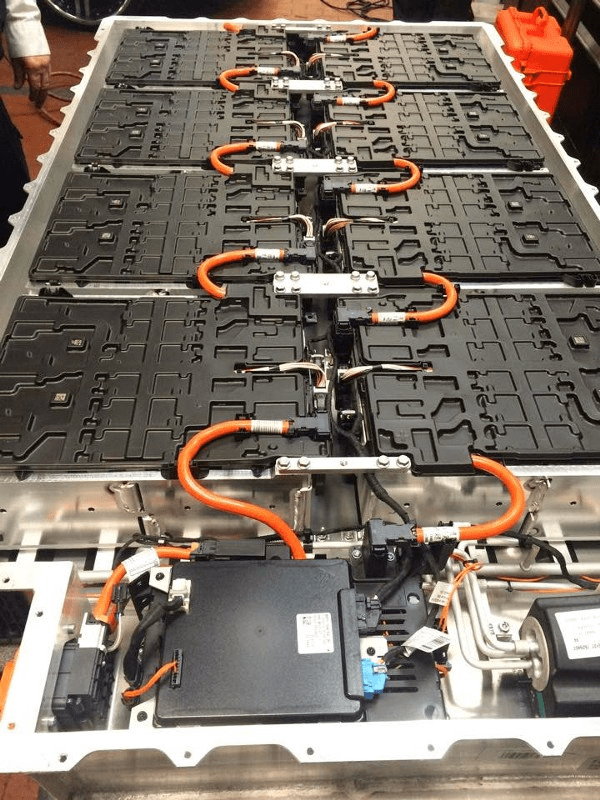
The advantages of the RIGID liquid cooling system are small size, light weight, low voltage, and safe and easy installation. The compact liquid cooling system generates a constant stream of low-temperature coolant that removes a relatively large amount of heat at a uniform rate. This type of system is closely matched to the battery and has channels around it for the coolant to circulate from the cooling system.
Little to no auxiliary power is required compared to air cooling; at the same time, because the coolant absorbs more heat than air, liquid cooling is more effective, making the process highly energy efficient.
At the same time, each battery can be equipped with a sensor to measure the voltage, capacity and temp inside the cell for monitoring the battery management system. This battery management system communicates with the cooling system and then adjusts to the needs of the situation.
Cold Plate Direct Cooling
RIGID DC Condensing Unit battery cooling system consists of a mini compressor, condenser and capillary. It is the world's smallest direct refrigeration unit. Its external size only 7.5" x 6.3" x 5.4 inch. The DC Condensing Unit is a sub-system, NO Evaporator. Clients need to connect it to their own evaporator or cold plate and then charge refrigerant. Then the evaporator closely through the battery pack and carries a flow of refrigerant to remove the heat from the battery cells.
Some Motor manufacturer's battery cell is about the size of a children’s book. Sandwiched between the cells is an aluminum cooling plate. Then there is one individual coolant path passing thru the cold plate to remove heat from the battery cell. Each battery cell is housed in a plastic frame. The frames with coolant plates are then stacked longitudinally to make the entire pack.
Since the cooling capacity and density of liquids is much higher than air, the amount of coolant required is much less than air cooling. Fluid refrigerant cooling is chosen as the coolant since it is a non-conductive liquid and is used in the battery industry. According to lab test, direct cooling shows very good performance for high heat generations.
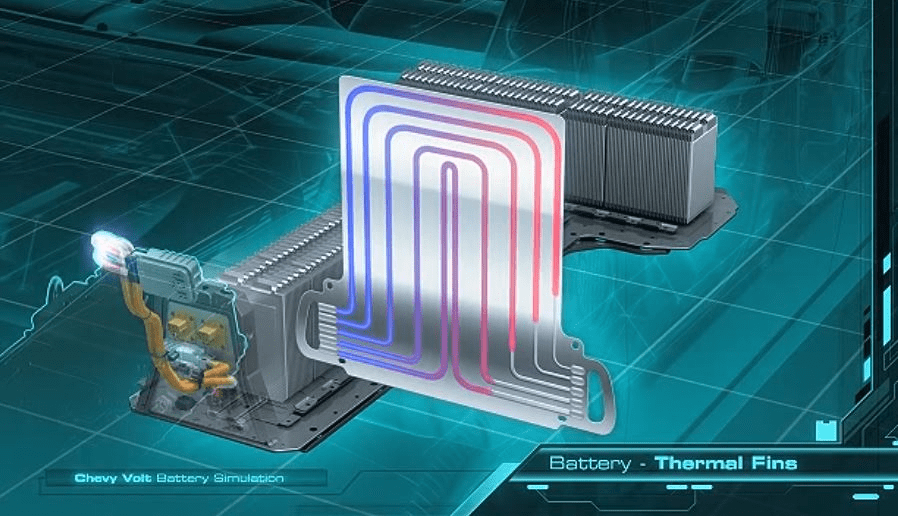
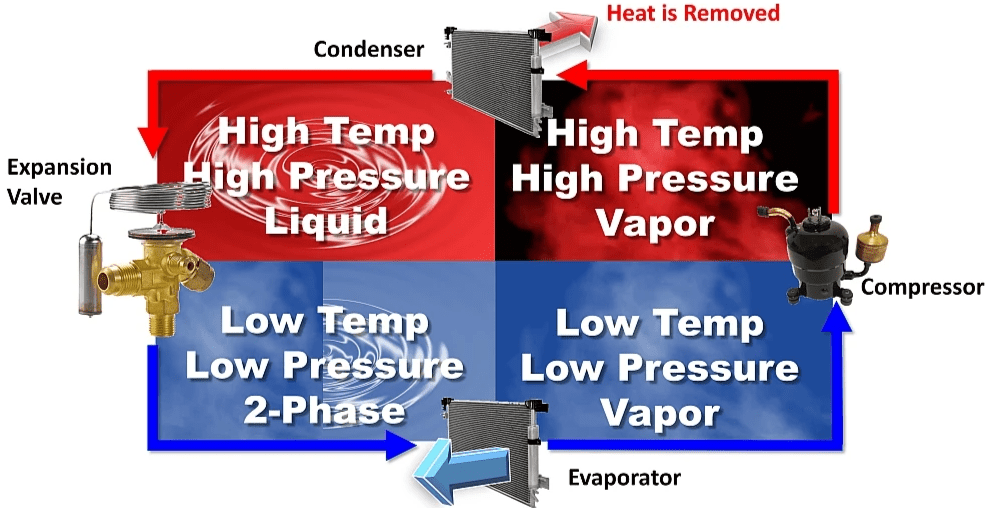
It is imperative that designers understand the cooling systems and the amount of heat generated by cells in the battery pack when designing thermal management solutions. Additionally, engineers must weigh various trade-offs and factors, such as manufacturing costs, packaging, energy efficiency, heat dissipation components' reliability, and a modular battery pack.
For the past 12 years, Rigid Technology has stood the test of time for the highest level of performance, quality, safety and innovation. All Rigid Standard Cooling Systems (1. Liquid Chiller System; 2. DC Condensing Unit; 3. Micro DC Aircon) are designed and manufactured with complete control of every step to ensure that Rigid's uncompromising standards for ultimate performance, unmatched reliability and highest durability are met. Besides standard chiller modules, Rigid also custom-made refrigeration units according to clients' demand.
RIGID product's pocket size and portability and very competitive price enable us is irreplaceable. RIGID Technology is well known for its unique design and high tech precision manufacturing, resulting in products that outperform and outlast any other brand on the market today.
