Introduction
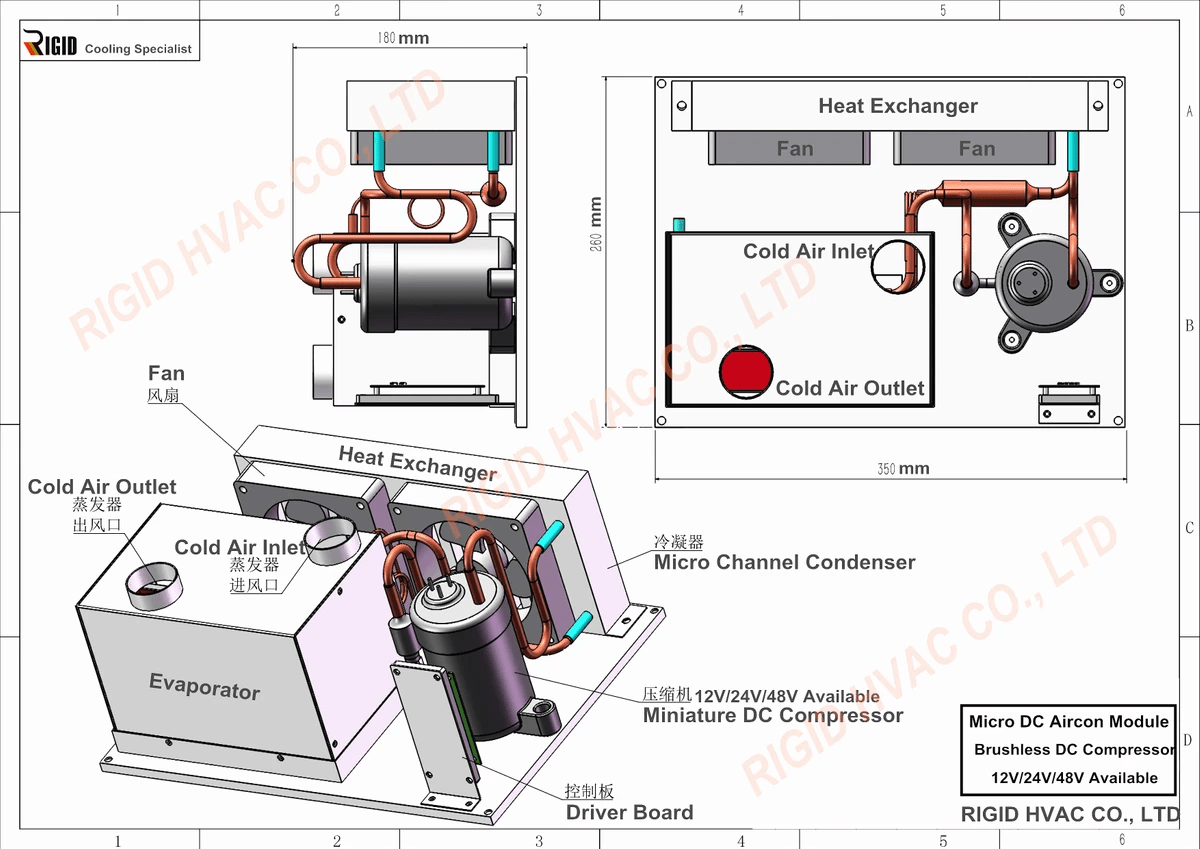
"RIGID is a miniature refrigerated compressor innovation leader in China. We keep looking for novel solutions in compact and portable cooling systems. We capture new technologies in mobile and compact cooling systems."
In the world of pharmaceuticals, maintaining the integrity and efficacy of products is paramount. This is where a robust pharmaceutical refrigeration solution comes into play, ensuring that temperature-sensitive medications and vaccines are stored under optimal conditions. Without effective cooling solutions, the risk of spoilage or degradation increases significantly, leading to potential health risks and financial losses.
Importance of Cooling Solutions in Pharmaceuticals
The importance of cooling solutions in pharmaceuticals cannot be overstated; they are essential for preserving the potency of drugs and ensuring patient safety. With many medications requiring strict temperature controls, understanding what liquid is used in refrigeration systems becomes critical for compliance and effectiveness. Moreover, improper storage can lead to catastrophic consequences, making reliable refrigeration a non-negotiable aspect of pharmaceutical operations.
Overview of Pharmaceutical Refrigeration Technology
Pharmaceutical refrigeration technology has evolved significantly over the years to meet the rigorous demands of the industry. From advanced vapor compression systems to innovative cryogenic freezing methods, various technologies cater to distinct needs within pharmaceutical settings. Understanding what are the requirements for a pharmaceutical refrigerator helps organizations choose appropriate systems that align with their specific operational goals.
Regulatory Standards for Temperature Control
Regulatory standards surrounding temperature control in pharmaceuticals are stringent and must be adhered to meticulously. Organizations must stay informed about these regulations to ensure compliance while also optimizing their processes through effective refrigeration techniques. By understanding what are the four types of refrigeration available and how they align with these standards, companies can better navigate this complex landscape while safeguarding their products.
Understanding Pharmaceutical Refrigeration Solutions
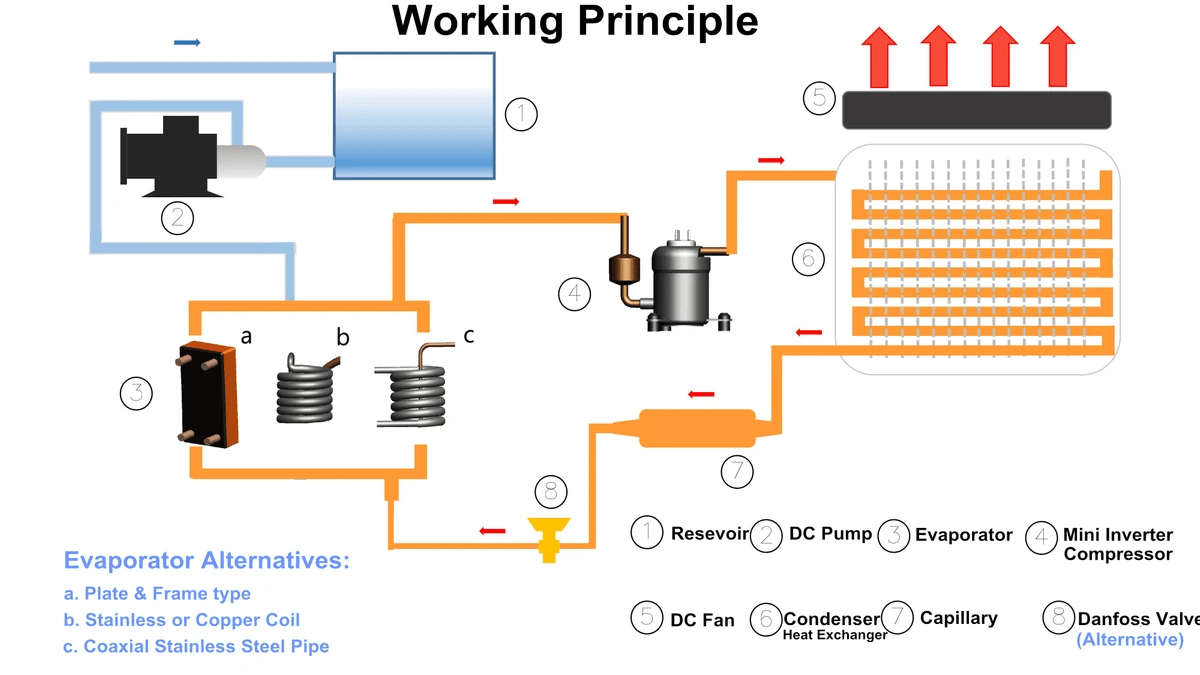
In the pharmaceutical industry, maintaining the integrity of products is paramount, and this is where a robust pharmaceutical refrigeration solution comes into play. These specialized systems are designed to ensure that temperature-sensitive medications and vaccines remain within strict temperature ranges throughout their lifecycle. Understanding these refrigeration solutions is essential for anyone involved in the storage and distribution of pharmaceuticals.
What is a Pharmaceutical Refrigeration Solution?
A pharmaceutical refrigeration solution refers to a tailored cooling system specifically designed to meet the unique needs of the pharmaceutical sector. Unlike standard refrigerators, these solutions prioritize precise temperature control, ensuring that sensitive products are stored under optimal conditions. They incorporate advanced technology to monitor temperatures continuously, which is crucial for compliance with regulatory standards.
Key Features of Effective Cooling Systems
Effective cooling systems in pharmaceuticals share several key features that distinguish them from conventional refrigeration methods. Firstly, they must maintain a consistent temperature range; fluctuations can compromise product efficacy and safety. Secondly, advanced monitoring systems are essential; they provide real-time data on temperatures and alert users to any deviations from set parameters—this ties directly into what liquid is used in refrigeration as well since different refrigerants have varying thermal properties.
Moreover, effective pharmaceutical refrigerators often include backup power systems to prevent any interruptions during electrical failures—after all, nobody wants a batch of vaccines going bad! These specifications ensure that every aspect of storage meets stringent industry requirements.
Comparison with Standard Refrigeration Techniques
When comparing pharmaceutical refrigeration solutions with standard refrigeration techniques, it becomes clear why specialized systems are necessary in this field. Standard refrigerators may not offer the precise temperature control required for sensitive pharmaceuticals; they often lack sophisticated monitoring capabilities as well. Additionally, while standard units might use common refrigerants effectively for food storage or general use, pharmaceutical applications demand specific liquids that comply with regulatory guidelines regarding safety and efficacy.
Furthermore, understanding what are the four types of refrigeration can also help inform choices about suitable technologies for different applications within pharmacy settings—whether it's vapor compression or cryogenic freezing methods tailored specifically for sensitive biological materials. Ultimately, investing in a dedicated pharmaceutical refrigerator means ensuring compliance with industry regulations while safeguarding valuable products through superior technology.
What Liquid is Used in Refrigeration?
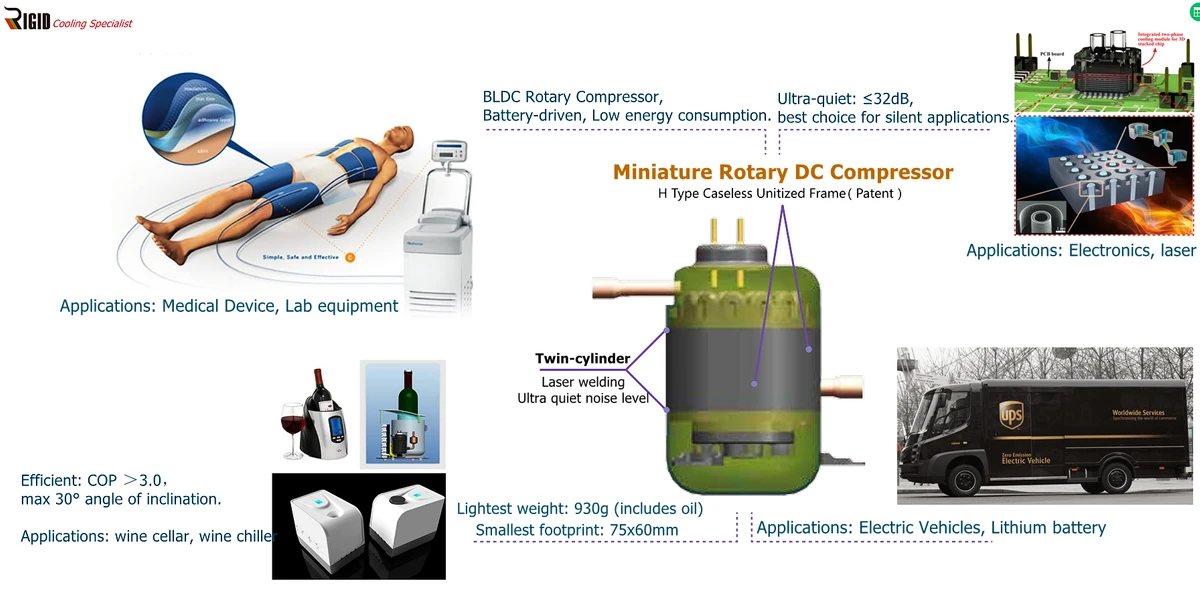
In the realm of pharmaceutical refrigeration solutions, the choice of refrigerant plays a pivotal role in ensuring that temperature-sensitive products are stored and transported effectively. Understanding what liquid is used in refrigeration can help stakeholders make informed decisions about their cooling systems. The right refrigerant not only affects efficiency but also compliance with regulatory standards, making it a crucial factor in maintaining optimal conditions for pharmaceuticals.
Common Refrigerants in the Pharmaceutical Industry
Hydrofluorocarbons (HFCs) have been widely used due to their favorable thermodynamic properties and lower ozone depletion potential compared to older substances like chlorofluorocarbons (CFCs). However, natural refrigerants such as ammonia and carbon dioxide are gaining traction for their environmental benefits, making them strong contenders for modern pharmaceutical refrigeration solutions.
Each type of refrigerant has its own set of characteristics that must be considered when determining what liquid is used in refrigeration. For instance, HFCs offer efficient cooling but come with concerns regarding global warming potential. On the other hand, while ammonia is highly efficient and cost-effective, it requires careful handling due to its toxicity.
Advantages and Disadvantages of Different Liquids
The advantages and disadvantages of various liquids used as refrigerants can significantly influence choices made by companies seeking effective pharmaceutical refrigeration solutions. For instance, HFCs provide excellent energy efficiency and stability at varying temperatures but contribute to greenhouse gas emissions when released into the atmosphere. Conversely, natural refrigerants like propane or CO2 are more environmentally friendly yet may have limitations regarding energy efficiency or safety concerns.
Moreover, specific applications may dictate which liquid is most suitable based on temperature control requirements for pharmaceuticals. The need for precise temperature management often means that traditional options might not suffice; thus alternatives must be explored diligently. Ultimately, understanding these nuances helps stakeholders align their choices with both operational needs and regulatory compliance.
Regulatory Considerations for Refrigerant Use
Regulatory considerations surrounding refrigerant use are paramount within the pharmaceutical industry due to stringent guidelines aimed at protecting public health and safety. Organizations such as the Environmental Protection Agency (EPA) enforce regulations that dictate which substances can be utilized based on their environmental impact—particularly concerning ozone depletion potential (ODP) and global warming potential (GWP). This means that companies must stay informed about evolving regulations when choosing what liquid is used in refrigeration systems.
Additionally, compliance with international standards such as those set forth by the World Health Organization (WHO) adds another layer of complexity when selecting a suitable refrigerant for pharmaceutical applications. Companies must ensure that their chosen solution meets both local and global regulatory requirements while maintaining efficiency in temperature control for pharmaceuticals. As regulations continue to evolve alongside technological advancements, staying ahead of these changes will be crucial for organizations aiming to maintain compliant operations.
Requirements for a Pharmaceutical Refrigerator
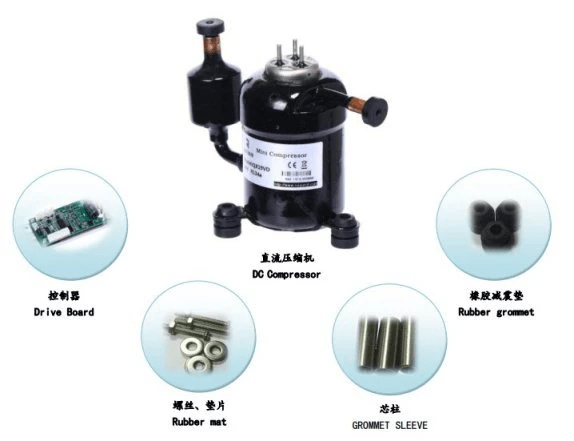
When it comes to ensuring the safety and efficacy of pharmaceutical products, understanding the requirements for a pharmaceutical refrigerator is crucial. These specialized refrigeration solutions must adhere to stringent specifications that guarantee optimal storage conditions. By focusing on compliance, temperature management, and backup systems, we can ensure that vital medications remain effective and safe.
Essential Specifications for Compliance
To meet regulatory standards, pharmaceutical refrigeration solutions must comply with specific specifications that ensure the integrity of stored products. These specifications typically include precise temperature ranges, humidity control, and robust monitoring systems. Additionally, manufacturers must provide documentation proving that their equipment meets all necessary industry regulations.
Compliance isn't just about ticking boxes; it's about safeguarding public health. For instance, if a pharmaceutical refrigerator doesn't maintain the required temperature range consistently, it could lead to compromised medications—an outcome no one wants to face. Thus, understanding what are the requirements for a pharmaceutical refrigerator helps in selecting the right equipment for your needs.
Temperature Range and Monitoring Systems
The ideal temperature range for pharmaceuticals varies depending on the type of product being stored; however, most require temperatures between 2°C to 8°C (36°F to 46°F). Advanced monitoring systems play an essential role in maintaining this range by providing real-time data on temperature fluctuations and alerting personnel if conditions deviate from set parameters. This proactive approach ensures that any potential issues are addressed before they jeopardize product integrity.
What is the temperature control for pharmaceuticals? It involves not only maintaining consistent temperatures but also implementing fail-safes like alarms or alerts when thresholds are breached. With precise monitoring technologies now available—like wireless sensors and cloud-based data logging—pharmaceutical companies can better manage their refrigeration solutions with ease.
Importance of Backup Power Systems
In an industry where every degree counts, having a reliable backup power system is non-negotiable for any pharmaceutical refrigerator. Power outages or equipment failures can lead to drastic temperature changes that compromise sensitive products—think vaccines or biologics! Therefore, incorporating uninterruptible power supplies (UPS) or generators into your cooling strategy is crucial.
Backup systems serve as an insurance policy against unforeseen circumstances; they ensure continuous operation even during power disruptions or technical malfunctions. In addition to protecting valuable inventory from spoilage due to inadequate cooling conditions, these systems contribute significantly towards compliance with regulatory standards in pharmaceutical refrigeration solutions. Ultimately, investing in robust backup power options can save time and money while preserving product quality.
Four Types of Refrigeration Explained
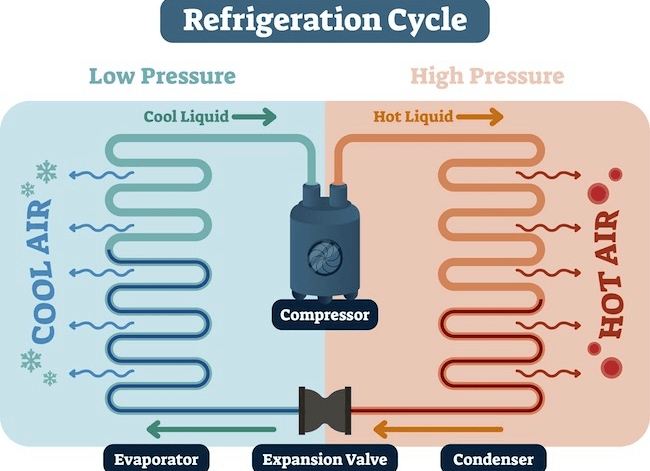
In the realm of pharmaceutical refrigeration solutions, understanding the various types of refrigeration technologies is crucial. Each type has its unique methodology and application, which can significantly impact the efficacy of temperature control for pharmaceuticals. This section will delve into four distinct refrigeration methods: vapor compression, absorption, thermoelectric cooling, and cryogenic freezing.
Vapor Compression Refrigeration
Vapor compression refrigeration is the most commonly used method in pharmaceutical settings. This system operates by compressing refrigerant vapor, which then condenses into a liquid, absorbing heat from the surrounding environment in the process. The efficiency and reliability of vapor compression make it a go-to solution for maintaining optimal temperature conditions in pharmaceutical refrigerators.
One key advantage of this method is its ability to achieve low temperatures quickly and maintain them consistently—critical factors when discussing what are the requirements for a pharmaceutical refrigerator. Additionally, vapor compression systems are relatively easy to maintain and repair compared to other types. However, they do require specific refrigerants that must comply with regulatory standards regarding what liquid is used in refrigeration.
Absorption Refrigeration
Absorption refrigeration offers an alternative approach that relies on heat rather than mechanical energy to cool substances. This method typically uses a refrigerant absorbed into a liquid solution; when heated, it evaporates and is later condensed back into liquid form by releasing heat elsewhere. It’s particularly useful in locations where electricity supply may be inconsistent or unavailable.
While absorption systems can be less efficient than their vapor compression counterparts, they provide unique advantages like quieter operation and reduced environmental impact—an important consideration given regulatory pressures on refrigerant use in pharmaceuticals. Moreover, they can utilize various energy sources such as natural gas or solar power to operate effectively. Thus, understanding absorption refrigeration adds another layer to your knowledge about what are the four types of refrigeration available today.
Thermoelectric Cooling
Thermoelectric cooling employs solid-state devices known as Peltier elements that create a temperature differential when an electric current passes through them. This technology offers precise temperature control for pharmaceuticals without moving parts or harmful refrigerants commonly found in traditional systems—making it an eco-friendly option worth considering for specialized applications.
Despite these benefits, thermoelectric cooling systems often struggle with larger-scale applications due to limited cooling capacity compared to other methods like vapor compression or absorption systems. However, they excel in scenarios requiring compact solutions where space is at a premium—ideal for small pharmaceutical refrigerators needing stringent temperature management without bulky equipment involved! Understanding this technology's potential helps clarify what are the requirements for a pharmaceutical refrigerator tailored towards niche markets.
Cryogenic Freezing
Cryogenic freezing represents one of the most extreme forms of temperature control available today; it utilizes liquefied gases such as nitrogen or helium to achieve ultra-low temperatures necessary for preserving sensitive biological materials like vaccines or cell cultures effectively! The rapid cooling capabilities allow for minimal ice crystal formation within samples—a critical factor when discussing what liquid is used in refrigeration at these temperatures.
However, while cryogenic techniques offer unparalleled precision and effectiveness in preserving delicate materials over extended periods, they also come with significant operational costs and safety considerations due to their extreme nature! As such, careful planning around Pharmaceutical Refrigerator Specifications becomes paramount before implementing this advanced technology within any facility handling sensitive products demanding strict adherence to regulatory guidelines regarding storage conditions.
Temperature Control for Pharmaceuticals
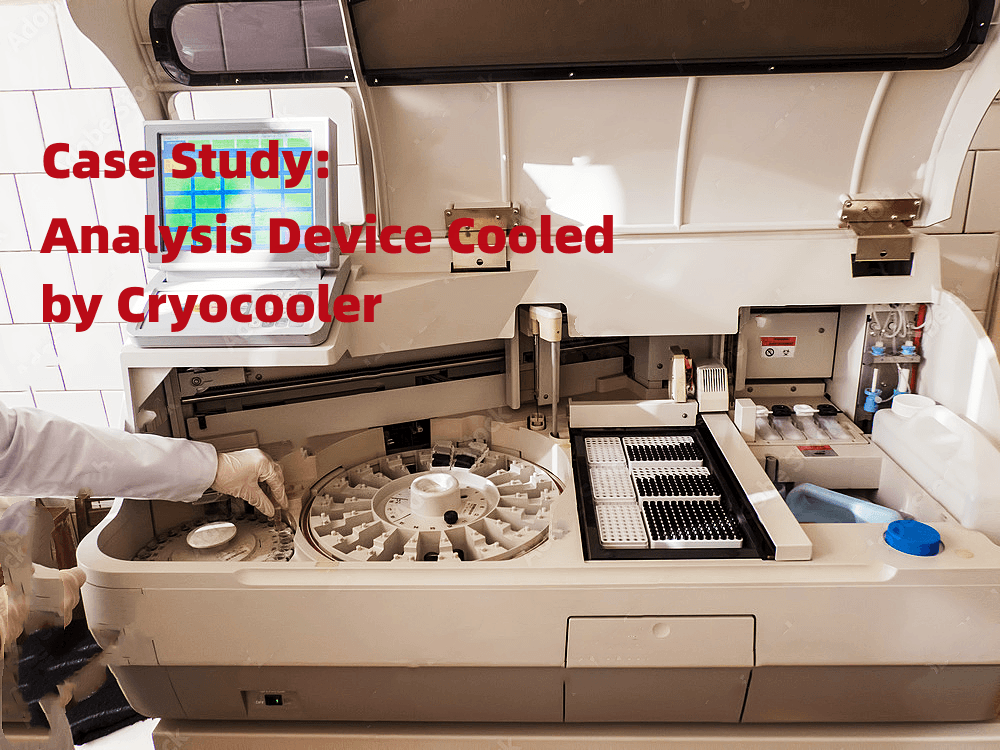
Temperature control is the backbone of effective pharmaceutical storage and distribution. The integrity of many medications hinges on maintaining precise temperatures, as even slight deviations can lead to degradation or loss of efficacy. Thus, a robust pharmaceutical refrigeration solution is not just a luxury; it’s an absolute necessity.
Importance of Precise Temperature Management
In the realm of pharmaceuticals, temperature management is critical for ensuring product safety and compliance with regulatory standards. Medications, especially biologics and vaccines, are often sensitive to temperature fluctuations; maintaining the right environment helps preserve their potency and shelf life. Therefore, understanding what is the temperature control for pharmaceuticals becomes essential for any operation dealing with these precious products.
Moreover, precise temperature management can prevent financial losses due to spoilage or recalls, which can be devastating in this industry. With the stakes so high, pharmaceutical companies must prioritize implementing effective cooling solutions that meet rigorous Pharmaceutical Refrigerator Specifications. This focus ensures that they not only comply with regulations but also uphold their commitment to patient safety.
Techniques for Ensuring Optimal Conditions
To achieve optimal conditions in pharmaceutical refrigeration solutions, several techniques are employed by industry professionals. First and foremost is regular monitoring using advanced sensors that provide real-time data on temperature variations inside storage units. These systems often come equipped with alarms that alert personnel immediately if temperatures stray from pre-set thresholds.
Another technique involves employing redundant systems such as backup power supplies to ensure continuous operation during outages or equipment failures—after all, no one wants to find out what happens when you ask what are the requirements for a pharmaceutical refrigerator! Additionally, routine maintenance checks on refrigeration units help identify potential issues before they escalate into costly problems.
Lastly, training staff on best practices in handling and storing pharmaceuticals can significantly enhance temperature control efforts. From understanding how long doors should remain open during restocking to using appropriate loading techniques within refrigerators—every action counts toward maintaining optimal conditions.
Innovations in Temperature Monitoring Technology
The landscape of temperature monitoring technology has evolved dramatically over recent years in response to industry needs for enhanced reliability and accuracy. New innovations include IoT-enabled devices that allow remote monitoring via smartphones or computers—a game-changer for those managing multiple locations or large inventories! This technology not only improves oversight but also provides valuable data analytics that can inform better operational decisions.
Moreover, advancements in smart sensors have led to more accurate readings and faster response times when deviations occur; these tools make it easier than ever to answer questions like what liquid is used in refrigeration? Some modern systems even utilize machine learning algorithms to predict potential failures before they happen based on historical data patterns—talk about being proactive!
Finally, integrating blockchain technology into supply chain logistics offers unprecedented traceability regarding temperature-controlled shipments from manufacturer to end-user. Such innovations promise greater accountability while ensuring compliance with stringent regulations surrounding pharmaceutical storage and transport.
Rigid's Role in Pharmaceutical Cooling
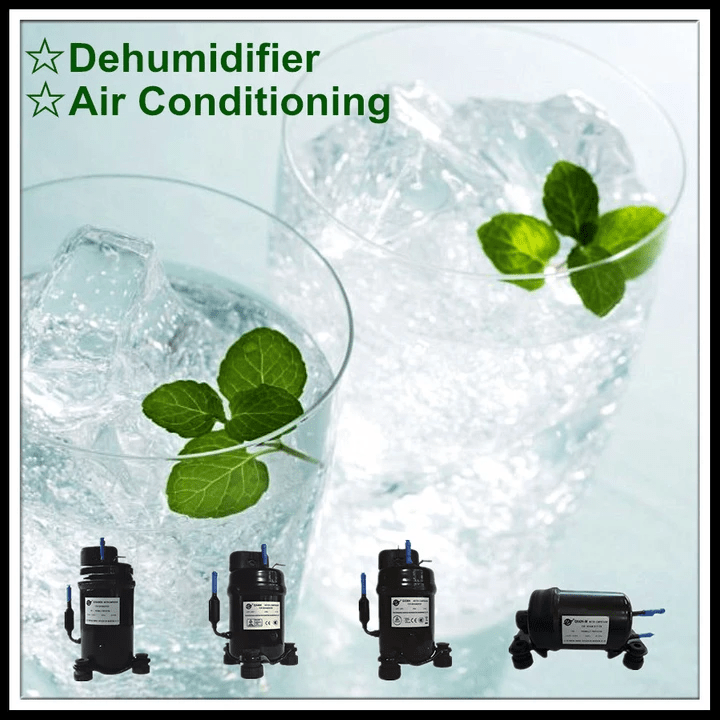
When it comes to pharmaceutical refrigeration solutions, RIGID stands out as a leader in the industry. With a keen understanding of what liquid is used in refrigeration systems and an unwavering commitment to quality, RIGID offers state-of-the-art cooling technologies designed specifically for the unique demands of pharmaceuticals. Their solutions are tailored to ensure compliance with stringent regulations while maintaining optimal conditions for sensitive products.
Overview of RIGID's Cooling Solutions
RIGID provides a comprehensive range of pharmaceutical refrigeration solutions that cater to various needs within the industry. Their systems are engineered with precision, ensuring that temperature control for pharmaceuticals is maintained at all times. By utilizing advanced technology and reliable components, RIGID guarantees that their refrigeration units meet the essential specifications required for any pharmaceutical refrigerator.
In addition to standard offerings, RIGID also incorporates innovative features such as real-time monitoring and alerts, which are crucial for ensuring product integrity. These enhancements make their cooling systems not just functional but also user-friendly and efficient. As a result, clients can focus on their core operations without worrying about temperature fluctuations or equipment failures.
Custom Solutions for Unique Pharmaceutical Needs
Recognizing that one size does not fit all in the pharmaceutical sector, RIGID excels at providing custom solutions tailored to unique requirements. Whether it's specific temperature ranges or specialized monitoring systems, they work closely with clients to develop bespoke pharmaceutical refrigeration solutions that align with their operational needs and regulatory standards. This level of customization ensures that each solution effectively addresses what are the requirements for a pharmaceutical refrigerator.
Furthermore, by leveraging their extensive expertise in various types of refrigeration—such as vapor compression and cryogenic freezing—RIGID can offer guidance on selecting the most appropriate system based on individual circumstances. This adaptability not only enhances performance but also fosters long-term partnerships built on trust and reliability within the industry.
Client Testimonials and Case Studies
RIGID's reputation as a leader in pharmaceutical cooling is further solidified through numerous client testimonials highlighting successful implementations of their refrigeration solutions. Many clients praise how RIGID’s systems have transformed their operations by improving efficiency while ensuring compliance with regulatory standards related to temperature control for pharmaceuticals. These positive outcomes serve as compelling evidence of how effective these custom solutions can be.
Case studies reveal remarkable improvements in product stability and shelf life thanks to optimized cooling environments provided by RIGID’s technology. Clients often note how these advancements have significantly reduced waste associated with temperature excursions—an issue frequently faced when using inadequate commercial refrigerators instead of dedicated pharmaceutical units like those offered by RIGID.
In summary, whether you’re grappling with what liquid is used in refrigeration or seeking clarity on what are the four types of refrigeration available today, partnering with RIGID ensures you receive top-notch support tailored specifically for your needs within the pharmaceutical landscape.
Conclusion
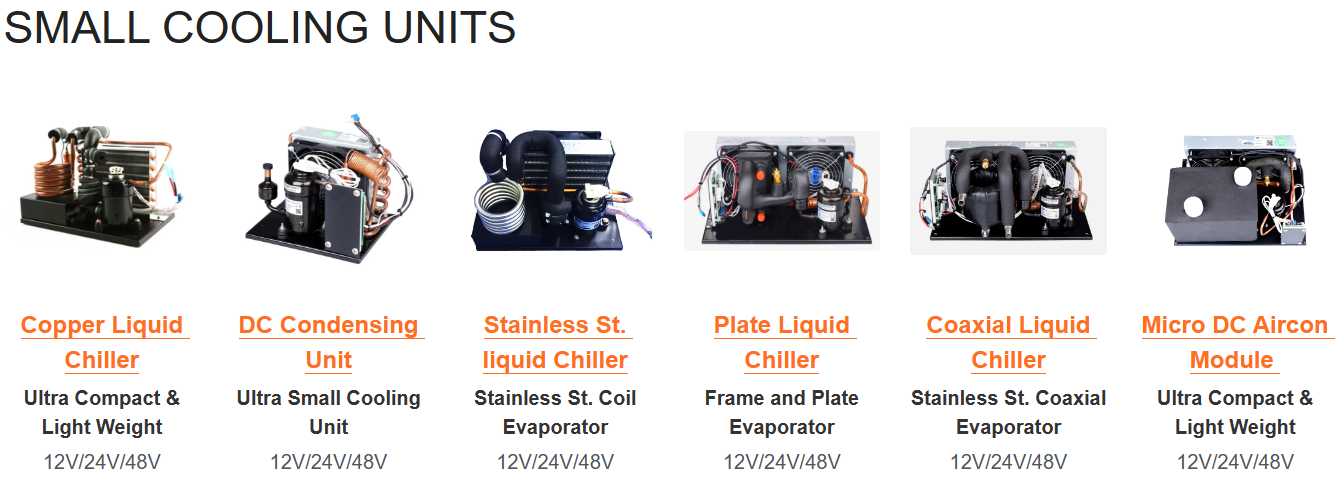
In the intricate world of pharmaceuticals, selecting the right pharmaceutical refrigeration solution is paramount to maintaining product integrity and compliance. With a diverse array of options available, it's essential to understand what liquid is used in refrigeration and how it impacts the effectiveness of these systems. As we move forward, keeping abreast of regulatory standards and technological advancements will ensure that pharmaceutical companies can confidently navigate their cooling needs.
Choosing the Right Pharmaceutical Refrigerator
Choosing the right pharmaceutical refrigerator requires a comprehensive understanding of pharmaceutical refrigerator specifications tailored to your unique needs. Factors such as temperature control for pharmaceuticals, energy efficiency, and capacity play critical roles in this decision-making process. Additionally, considering what are the requirements for a pharmaceutical refrigerator—like backup power systems and monitoring capabilities—ensures that your solution remains reliable under all circumstances.
Staying Compliant with Industry Regulations
Staying compliant with industry regulations is not just about ticking boxes; it’s about safeguarding public health and ensuring product efficacy. Understanding what liquid is used in refrigeration can also influence compliance since certain refrigerants may be subject to stricter regulations than others. By regularly updating knowledge on regulatory standards and integrating them into your operations, you can avoid costly penalties while enhancing your reputation in the industry.
Future Trends in Pharmaceutical Cooling Technology
The future trends in pharmaceutical cooling technology are poised to revolutionize how we think about temperature management within this sector. Innovations such as smart monitoring systems that provide real-time data on temperature fluctuations will enhance overall efficiency and reliability of pharmaceutical refrigeration solutions. Moreover, exploring what are the four types of refrigeration—vapor compression, absorption, thermoelectric cooling, and cryogenic freezing—will help businesses adapt their strategies to leverage emerging technologies effectively.